Every 11 seconds, a perma lubrication system is installed or exchanged, worldwide. Manual lubrication is a thing of the past! Today, anyone looking for safe, effective and long-term economical lubrication of equipment takes advantage of automatic lubrication. perma offers ideal technical and economical solutions for any lubrication point.
300
55 mill.
122 mill. €
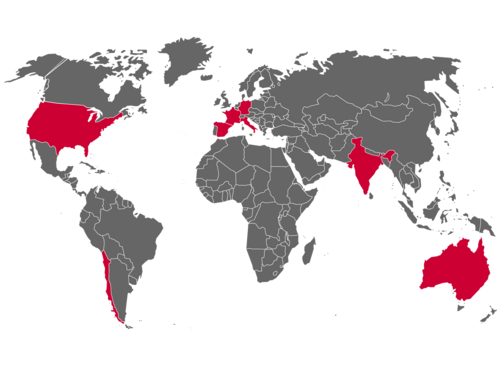
Subsidiaries
In addition to the headquarters in Euerdorf, Germany, seven further locations have been successfully established worldwide over the years.
For contact details of our subsidiaries in the US, South America, Spain, Italy, France, India and Australia, please click here.
Advantages at a glance
Technical aspects
perma simplifies maintenance work
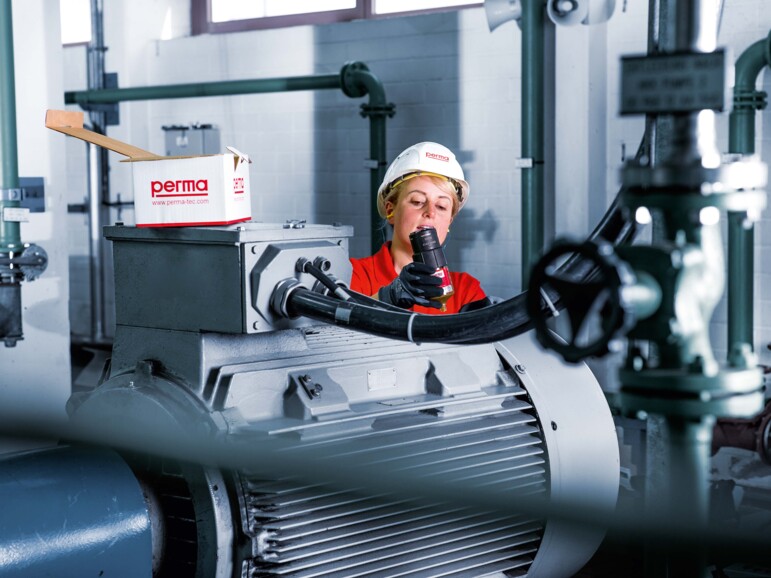
Equipment availability
perma helps prevent up to 75 % of roller bearing failures
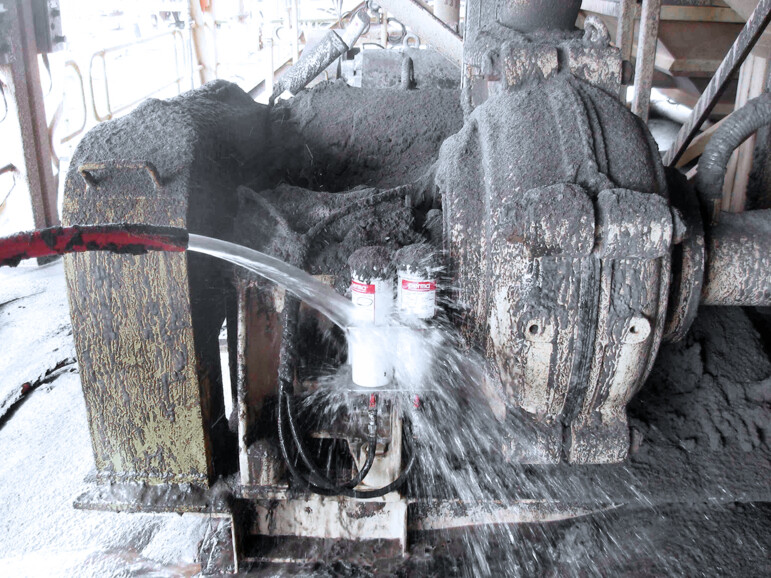
Cost effectiveness
perma reduces costs by up to 25 %
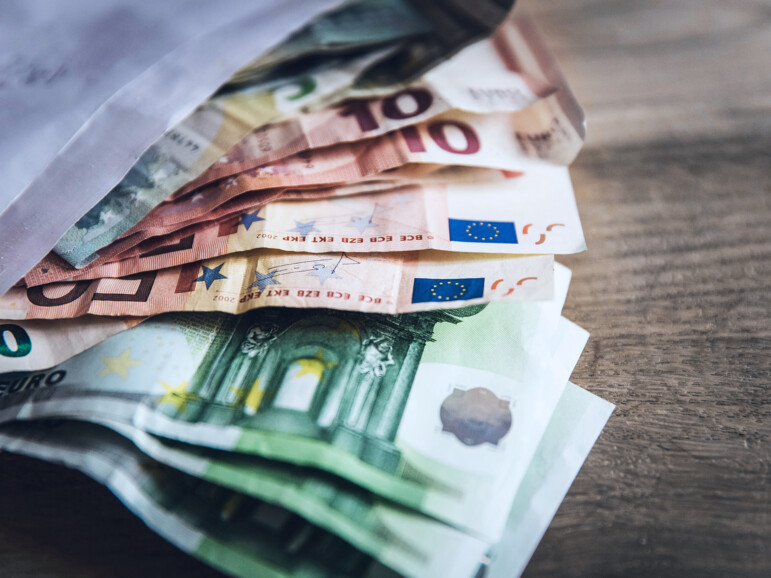
Workplace safety
perma reduces the risk of accidents by up to 90 %
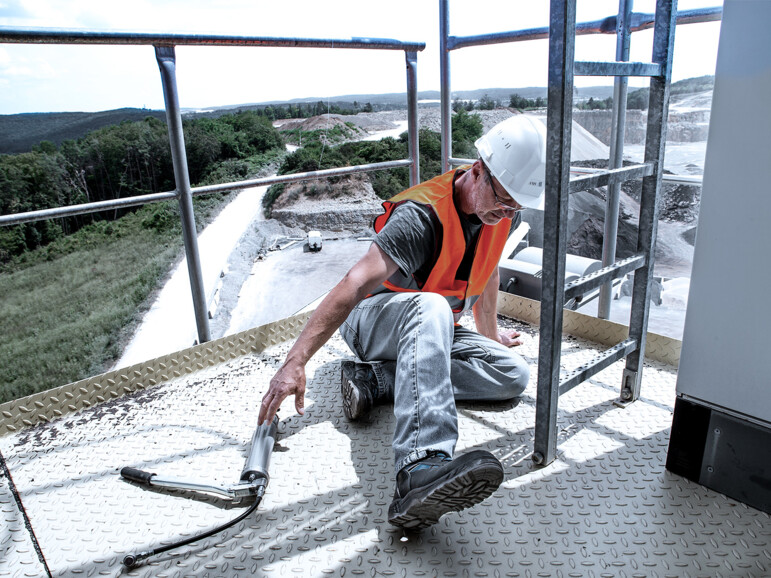
Environmental protection
perma – certified environmental management system
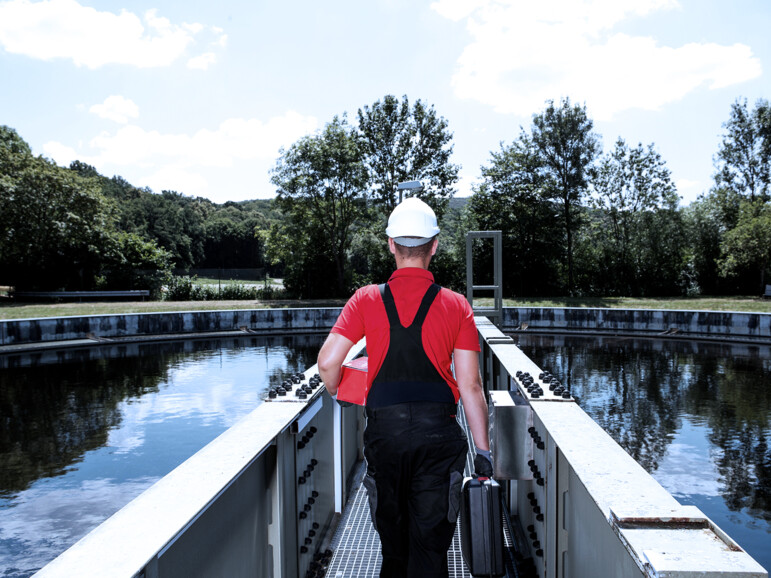
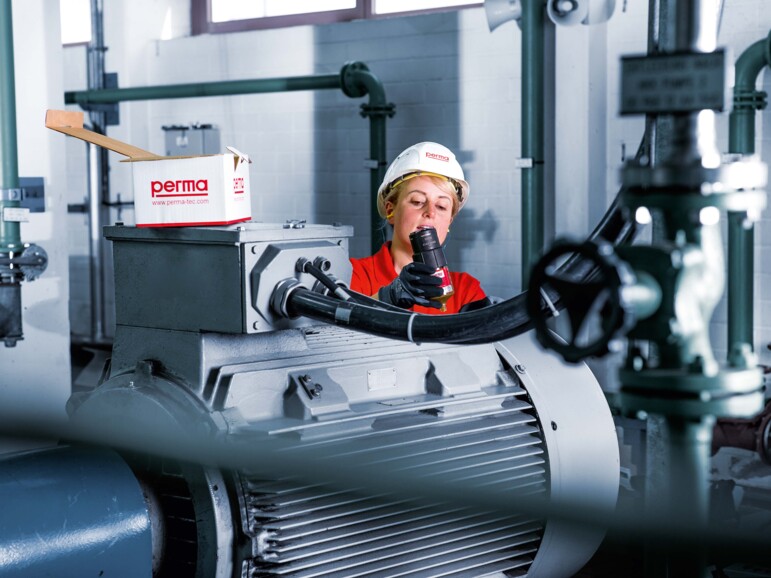
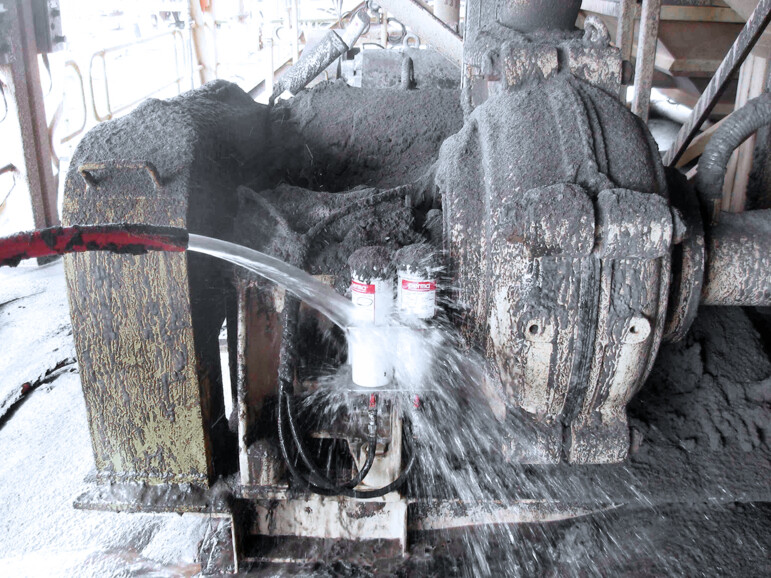
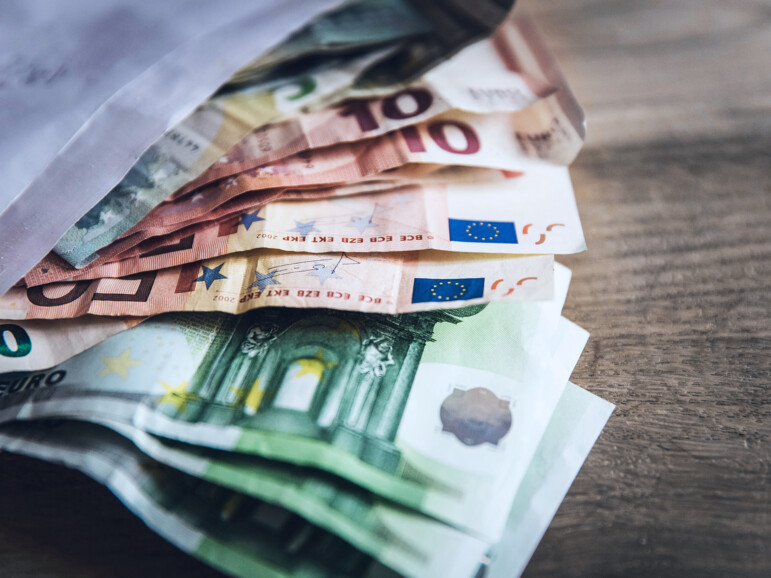
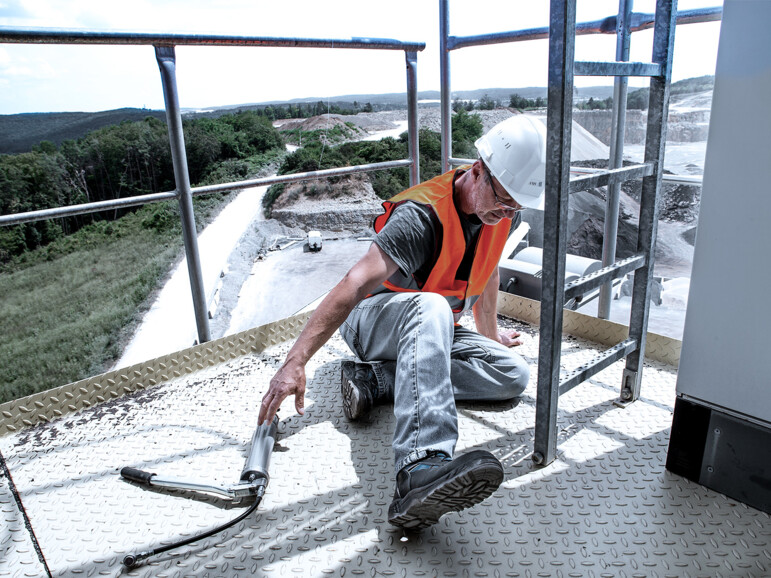
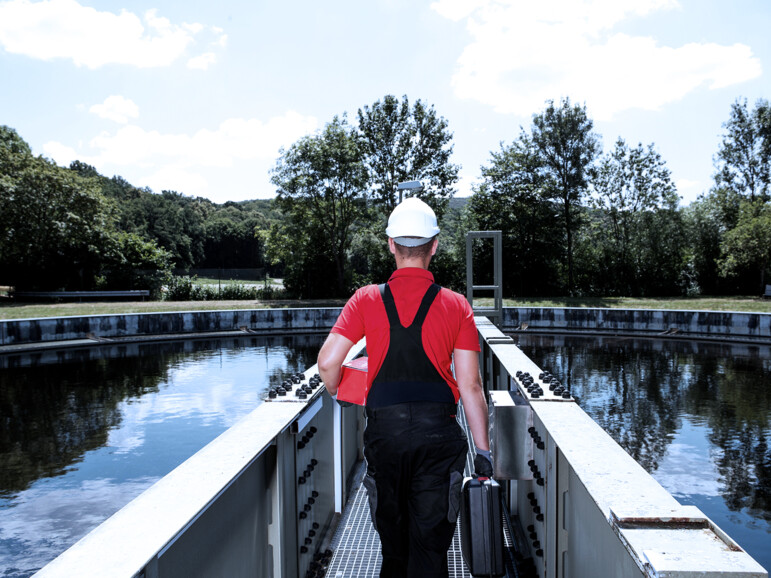
Our Corporate Philosophy
History
For more than 60 years, perma has stood for innovative and creative lubrication solutions.
perma single- and multi-point lubrication systems are used in almost all types of industries and applications around the world.
perma’s leadership in the single-point lubrication market is based on numerously patented and specifically certified products. All perma products are developed, tested and manufactured in the company’s headquarters in Germany and meet the quality standard “Made in Germany”.
With many years of experience, a global network of own subsidiaries and competent partners around the world, perma can offer customers many solutions that meet the highest technical requirements.
Foundation of metal goods factory for household and kitchen appliances in Bad Kissingen
Invention and patenting of perma CLASSIC single-point lubrication system
Sale / acquisition by private investment group
New management and extensive reorganisation
Foundation of subsidiaries H-T-L perma
Change of company name to perma-tec GmbH & Co. KG
New production and warehouse building as well as an office building extension
Completion of additional warehouse / office building
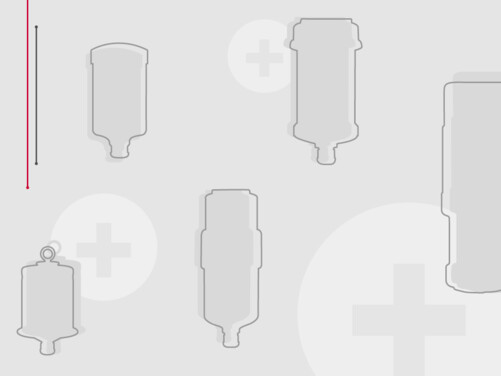
Advantages for our customers
At perma, the customer is at the centre. We believe that satisfied customers are the key to our success. That’s why we strive to prioritise your needs and expectations in all our actions.
Our Team
Our employees are our greatest strength. Discover the team that powers perma’s global leadership in single-point lubrication.
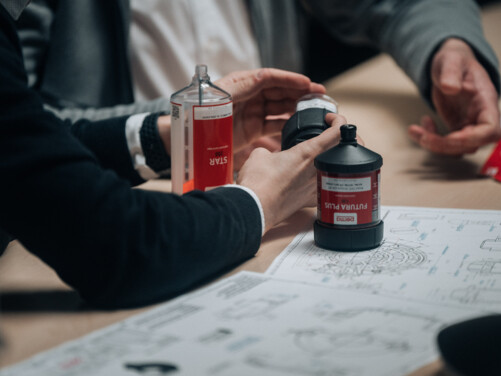
Certificates and Memberships
perma-tec has been certified for the introduction and implementation of a quality and environmental management system according to the DIN EN ISO 9001 and DIN EN ISO 14001 standards in the area of development, production and distribution of perma lubrication systems.
The cerficates can be downloaded here: DIN EN ISO 9001, DIN EN ISO 14001.
The latest certificates can be downloaded here:
The following perma products are UL certified:
perma STAR VARIO
perma PRO
The European Power Transmission Distributors Association (EPTDA) is the largest organisation of distributors and manufacturers of power transmission and motion control products in Europe. It represents over 190 companies of the industry. EPTDA is dedicated to providing its members with information, education and business tools required to profitably meet the needs of the industrial market place. The EPTDA offers a unique platform for productive communication and networking between distributors and manufacturers on a senior management level.
perma-tec has received the TISAX-certificate and thus complies with the official security standards required when working with customers and suppliers in the automotive industry.
TISAX stands for „Trusted Information Security Assessment Exchange” and is an important requirement for secure data exchange. Leading the development of this standard for information security is the Association of the Automotive Industry (VDA).
TISAX Certificate
The ENX Association supports with TISAX (Trusted Information Security Assessment Exchange) on behalf of VDA the common acceptance of Information Security Assessments in the automotive industry. The TISAX Assessments are conducted by accredited audit providers that demonstrate their qualification at regular intervals. TISAX and TISAX results are not intended for general public.
For perma-tec confidentiality, availability and integrity of information have great value. We have taken extensive measures on protection of sensitive and/or confidential information.
Therefore, we follow the question catalogue of information security of the German Association of the Automotive Industry (VDA ISA). The Assessment was conducted by an audit provider, in this case the TISAX audit provider DEKRA. The result is exclusively retrievable over the ENX Portal. The certification is valid worldwide and subject to regular assessments for recertification.
Energy policy according to ISO 50001
The energy policy plays a special role in the production, storage, transport, use and disposal of our products. The reduction of the usage of energy and resources is to be constantly promoted. Each employee is personally required to take into account the aspects of our energy policy, which are specified, implemented and regularly reviewed by the energy representative.
perma-tec has been certified for the introduction and implementation of an energy management system according to the DIN EN ISO 50001:2018.
The certificate can be downloaded here.
Both certificates were issued because perma complies with the EN ISO / IEC 80079-34: 2020 standard.