Electric motors are used in many different applications.
An electric motor is designed to convert electrical into mechanical energy. Efficient lubrication and maintenance are essential for reliable operation of electric motors. Still, many of them are lubricated at irregular intervals as they are located in areas which are difficult to reach or dangerous. Failure to adhere to manufacturer specifications frequently leads to damage and breakdowns caused by bearing over-lubrication or lubrication starvation.
Challenges
During manual lubrication, the grease is applied in uneven amounts. A large quantity of lubricant is introduced at one time. This leads to a temporary over-lubrication of bearings. Ignoring the recommended relubrication intervals leads to lubrication starvation.
Relubrication during running operations (manufacturer recommendations) jeopardises maintenance staff. The risk of accidents increases when people spend time in dangerous or hard-to-reach areas.
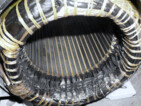
Bearing heating and possible fire hazard since it takes hours to distribute excess grease
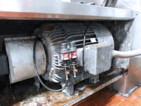
Possible shut-off with temperature monitoring
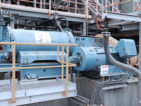
Bearing damage due to lubrication starvation results in unscheduled machine downtimes and higher production costs
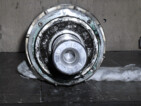
Increasing maintenance costs caused by premature wear
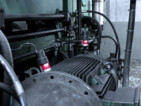
High accident risk

Motor shut-down when entering secured areas

Lubrication points
Lubrication points are located on the drive and non-drive end of electric motors. When relubricating, you must ensure that excess grease is discharged through the discharge openings, grease relief ports or grease traps. Bearings will overheat if grease cannot escape and / or if grease traps are filled up with used grease.
Solutions
Mount a perma lubrication system at the lubrication point. Depending on the conditions prevailing at the lubrication point, the perma lubrication system can either be mounted directly or remotely.
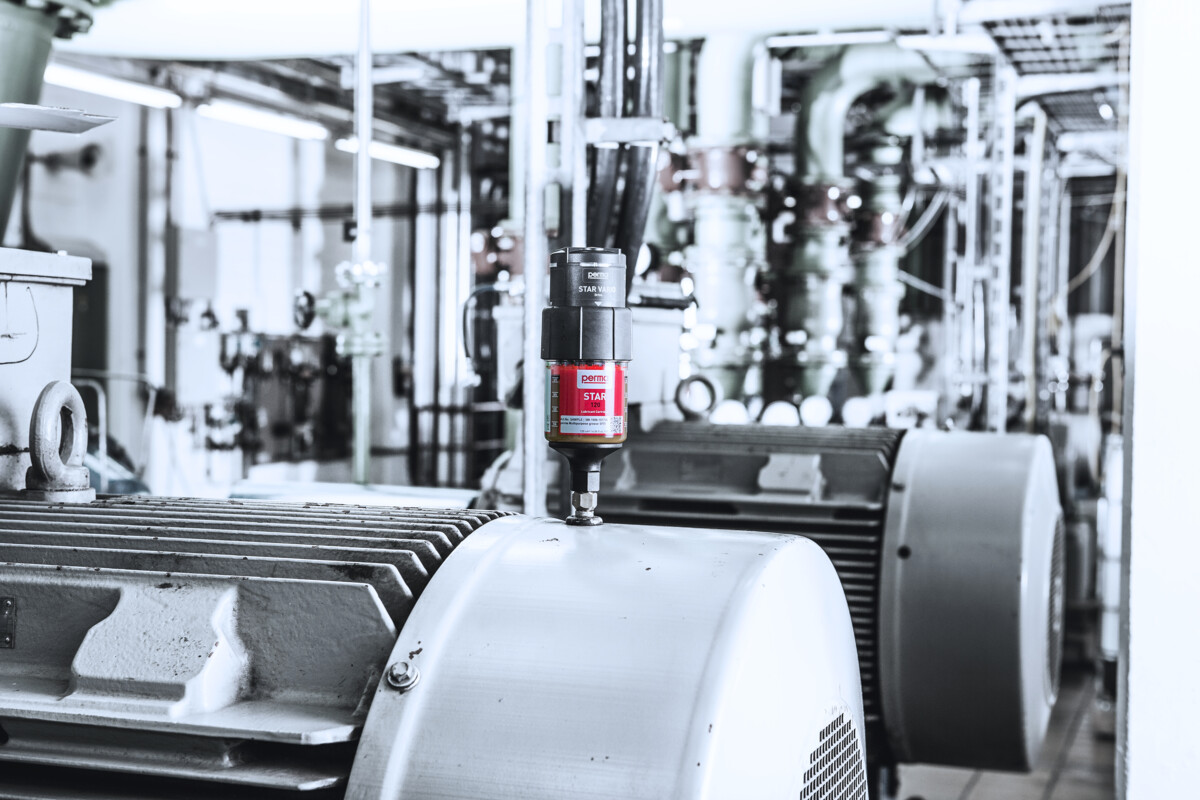
- Easy, quick mounting
- For lubrication points with little vibration / shocks
- For easy-to-reach, safe lubrication points
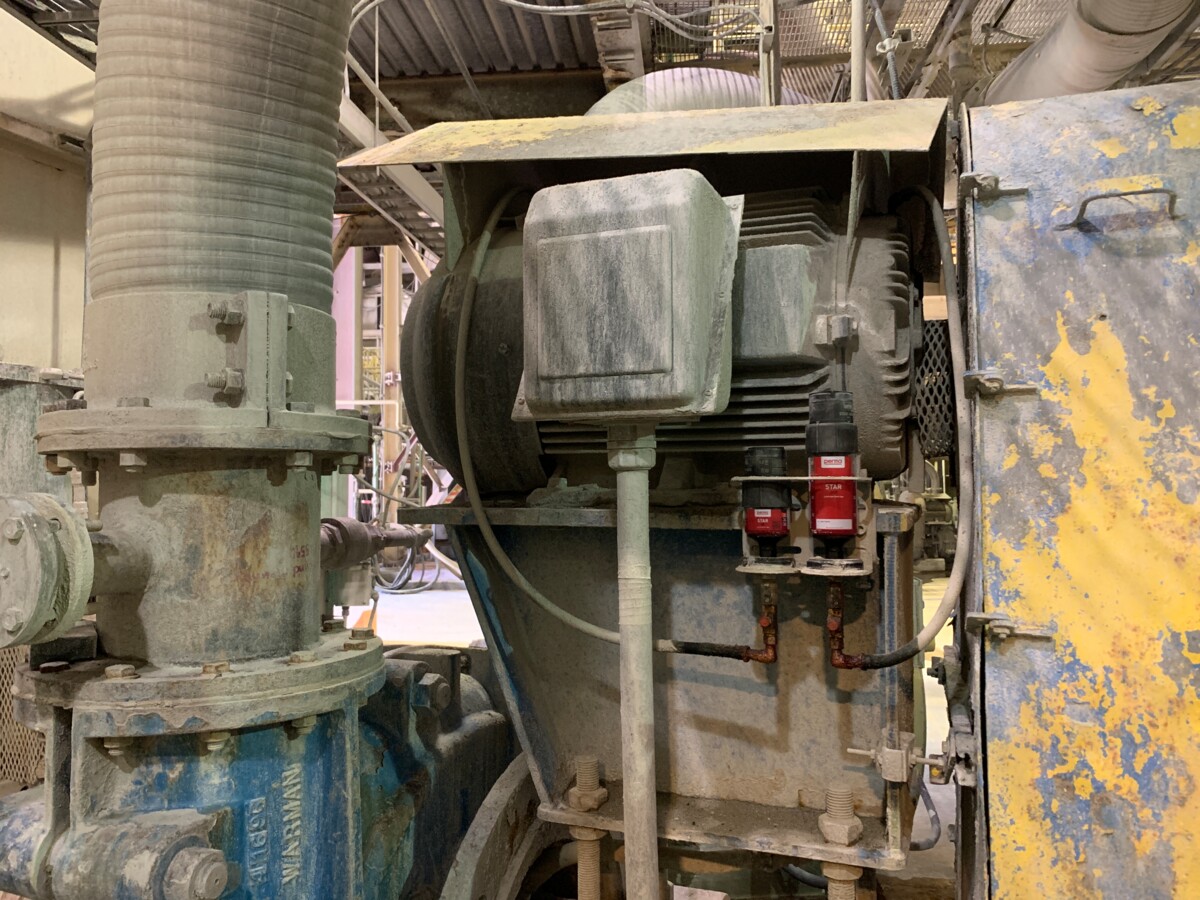
- For lubrication points with strong vibration / shocks (isolation of lubrication system)
- For lubrication points which are unsafe to access: Mounting in safe areas
- For hard-to-reach lubrication points
Any more questions?
Simply contact us by phone or email for an individual consultation on electric motors.
Advantages of automatic lubrication
Minimised overheating
Relubrication during running operation minimises overheating of bearings
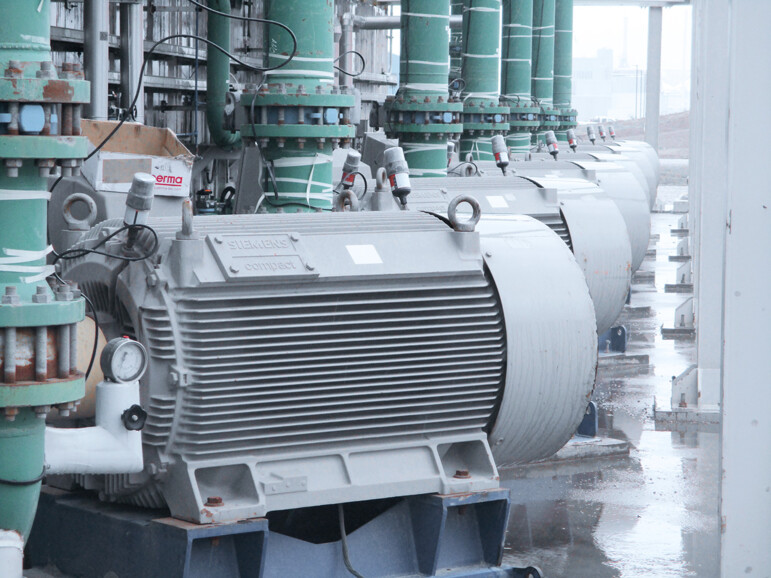
Predictable exchange intervals
Predictable exchange intervals with reduced material and personnel expenditure
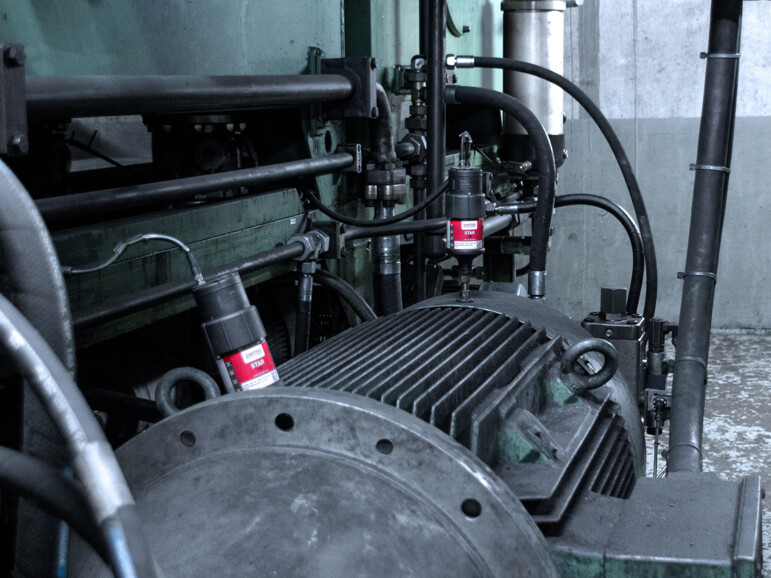
Workplace safety
Increased workplace safety due to automatic lubrication of hard-to-reach lubrication points
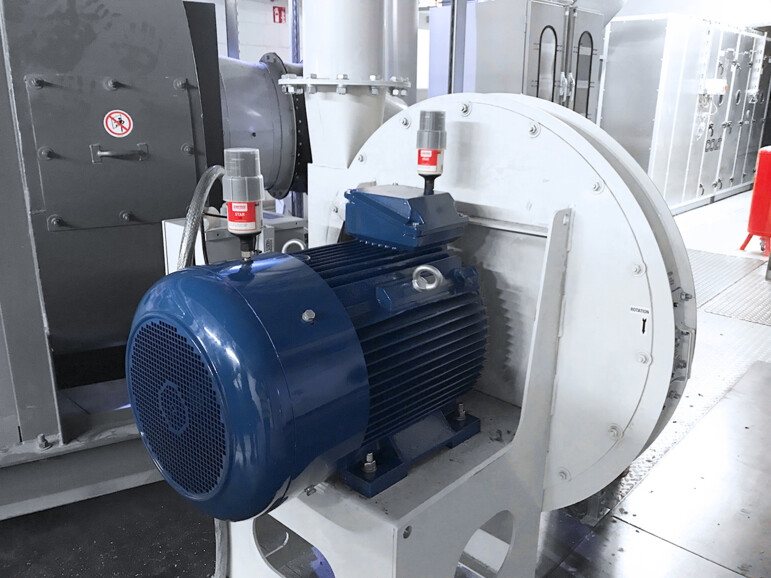
Lower environmental impact
Precise lubricant discharge lowers lubricant consumption and thereby environmental impact
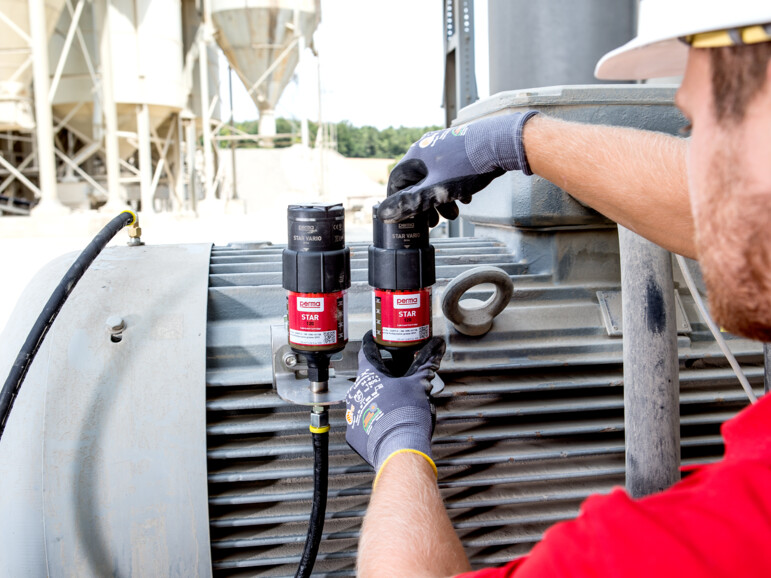
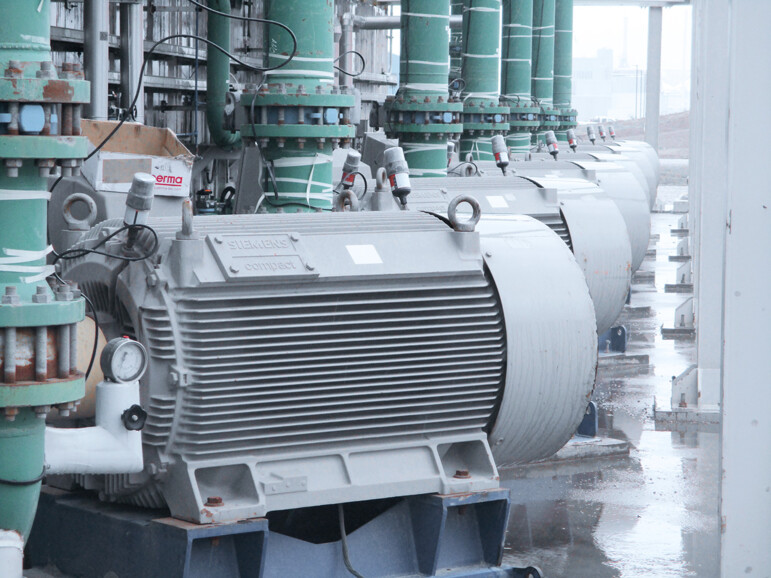
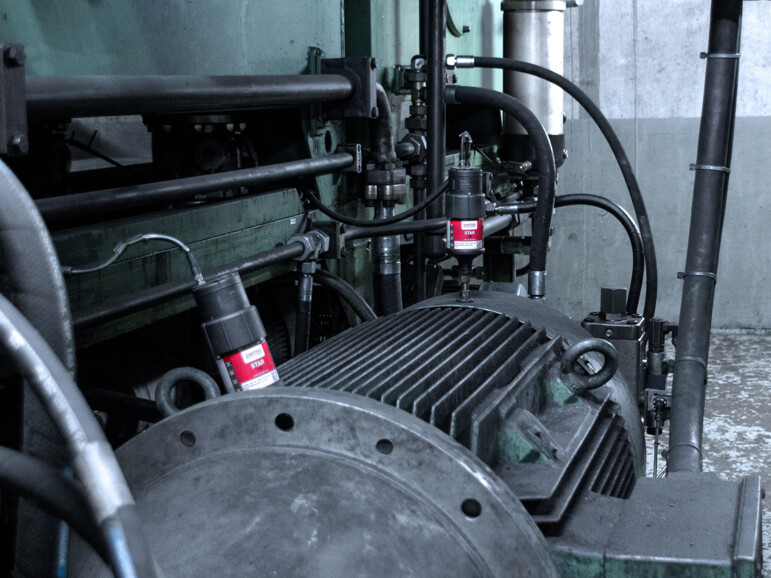
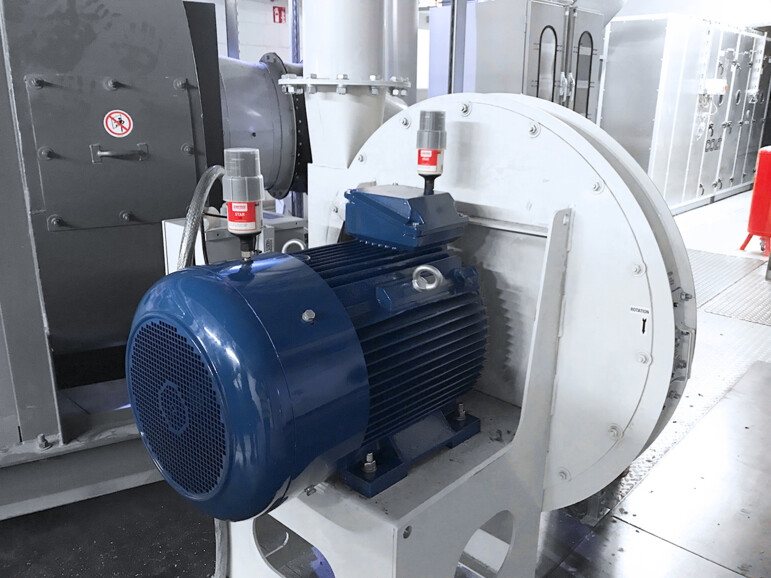
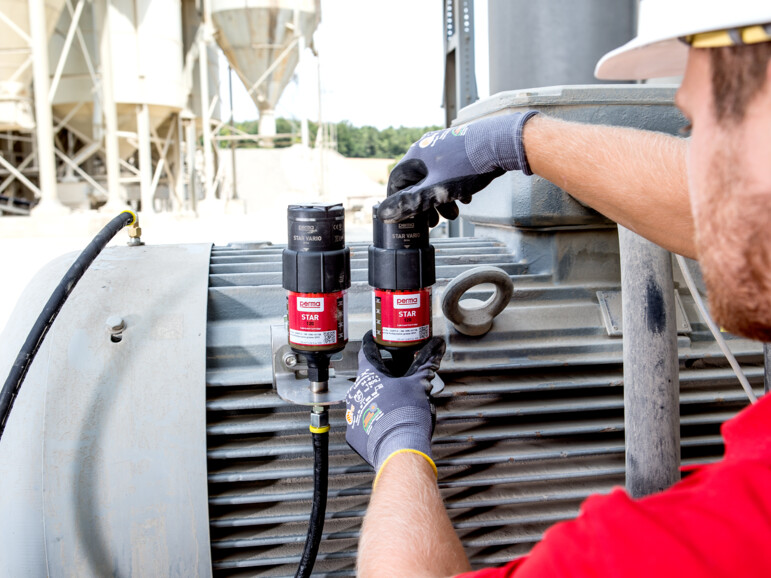