The design capacity of the Bad Kissingen sewage plant is 60,000 PE (population equivalent). The plant is located in the immediate vicinity of the river Franconian Saale. Bad Kissingen is a famous spa town with valuable mineral springs. The protection of these mineral springs is a great challenge for the sewage plant especially when the river floods.
“We have special overflow basins and pumping stations for floods” explains Alexander Pusch, Head of Wastewater Operations and Flood Protection at the sewage plant Bad Kissingen. Alexander Pusch and his team of 18 people are responsible for smooth plant operation. The problem with sewage treatment is that all important machine elements like roller- and sliding bearings, chains and spindles are constantly exposed to wastewater which carries dirt, phosphate or other chemicals. The challenging question is “how can the team guarantee trouble-free plant operation day and night even during extreme weather”.
“One important point is preventive and ongoing maintenance, especially the correct lubrication of machines and equipment”, says the manager. Sewage plant maintenance is one of the biggest cost factors besides personnel and energy costs. For this reason, maintenance must be as effective as possible. “We have been working with perma for many years. perma lubrication systems are used for the lubrication of different applications and we are very satisfied with the way they function and with their reliability” explains Alexander Pusch.
The function of perma lubrication systems
perma lubrication systems not only provide reliable lubrication for sewage plant equipment, they also effectively seal lubrication points and protect them against dirt and moisture. Longer discharge periods reduce maintenance costs and remote mounting with tube lines increases workplace safety because hard to reach lubrication points can be accessed safely. The exact lubricant dosing, matched to the actual lubricant requirement of individual applications, prevents contamination caused by over-lubrication and saves valuable resources. perma lubrication systems are filled with biodegradable lubricants for environmental protection.
Numerous applications for automatic lubrication systems
“We use these lubrication systems especially for the roller bearings in our aeration tanks or on the drive gear of surface aerators. In the scraper building, we have installed them on pumps and on the roller bearings of organic press scrapers. Outdoors, we use them on the sedimentation tank scrapers and on rope drum shafts. perma lubrication systems have proven to be extremely reliable despite the harsh operating conditions in our plant like high temperature fluctuations, dirt and moisture” says the manager.
He further explains: “In the outdoor area of the sewage treatment plant we mainly use the temperature independent precision system perma STAR VARIO. Inside, we use the perma FLEX since this system is available in different sizes which can be adjusted to meet the lubricant requirement of different equipment we have. All lubrication systems are self-sufficient. With perma lubrication systems, we were able to increase our equipment availability. All process steps operate reliable which reduces the workload for our maintenance team. This saves a lot of time and lowers operational costs. We are also very satisfied with the service from perma-tec.”
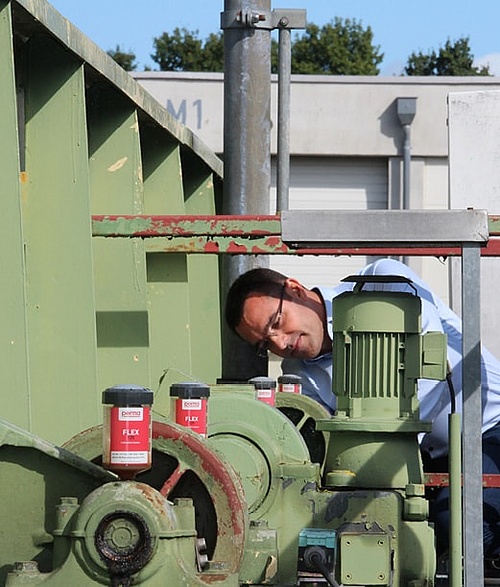